Product Safety
Consumer Products
Window Coverings
Window coverings are useful for privacy, light control and energy efficiency in our homes. However, they can pose significant danger, especially to children and pets, if they have cords that can form loops or strangulation hazards. To mitigate this danger, window covering manufacturers have been encouraged by standard to implement safety features, such as cord stops, cord cleats, and warning labels, in their products. Additionally, many manufacturers now offer cordless options, including motorized and retractable shades and blinds, which eliminate (or reduce) the risk of entanglement altogether. Well-designed window coverings prioritize safety by eliminating cords and incorporating proper guarding devices.
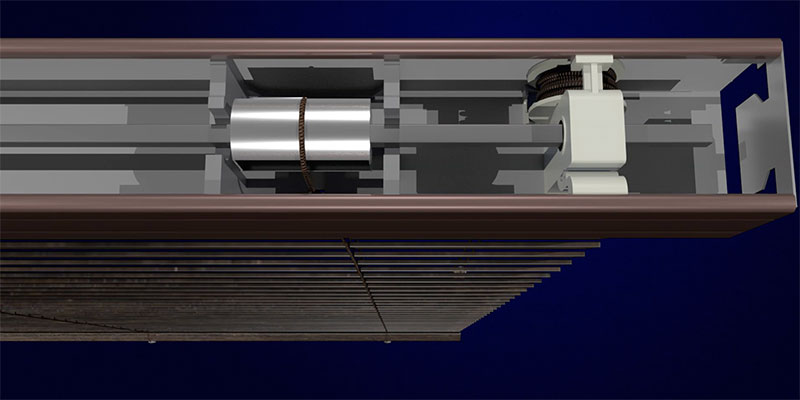
Furniture Products
The safety of furniture products is an essential consideration for manufacturers, retailers, and consumers. One of the primary safety concerns is the stability of furniture, particularly for items such as bookcases, dressers, and cabinets. These items can topple over if they are not adequately anchored to the wall or have a high center of gravity. Collapses can result in serious injury, particularly to children. Another safety concern is power furniture, which includes items such as recliners and adjustable beds. These products must be designed and tested to ensure that they do not malfunction or entrap children or animals, causing injury. Sharp edges on furniture can also pose a safety hazard, particularly for children. Manufacturers must take measures to round or dull edges to prevent cuts and bruises. In summary, safety in furniture products requires proper design, testing, and compliance with safety standards to prevent accidents and ensure consumer protection.
Pool Safety
Above ground pool ladder design plays a critical role in ensuring safety and preventing unauthorized access by young children into the pool area, as well as reducing the risk of tip-over related injuries. Manufacturers employ various safety features to achieve these goals, such as incorporating locking or removable steps, which can be detached or secured when the pool is not in use, effectively restricting access to the pool for young children. Additionally, non-slip surfaces on the steps and handrails contribute to improved traction and stability, reducing the likelihood of falls and injuries. Ladder stability is further enhanced by the use of wide, sturdy bases and durable materials, which minimize the risk of tip-overs during entry and exit. Some designs also incorporate safety barriers or gates, adding an extra layer of protection against unauthorized access. By combining these safety features with proper installation, above ground pool ladders can effectively mitigate the risk of accidents.
Sports & Recreational Products
The design and safety of recreational and sports products, particularly helmets, are of paramount importance in preventing injuries and ensuring the well-being of participants. Helmets serve as a critical line of defense against head injuries, such as concussions and skull fractures, which can occur during various sports and recreational activities. Manufacturers employ advanced engineering techniques and materials to create helmets that effectively absorb and distribute impact forces. This is achieved through features such as energy-absorbing foam liners, durable outer shells, and adjustable retention systems, which work in tandem to provide optimal protection and a secure fit. In addition, helmets are often tailored to the specific needs and risks associated with individual sports or activities, ensuring that the design provides adequate coverage and support for the areas most vulnerable to injury. To further enhance safety, helmets must adhere to stringent standards and undergo rigorous testing procedures to ensure their performance under various conditions. By investing in research and development, manufacturers continually strive to improve helmet designs and materials, making recreational and sports activities safer and more enjoyable for all participants.
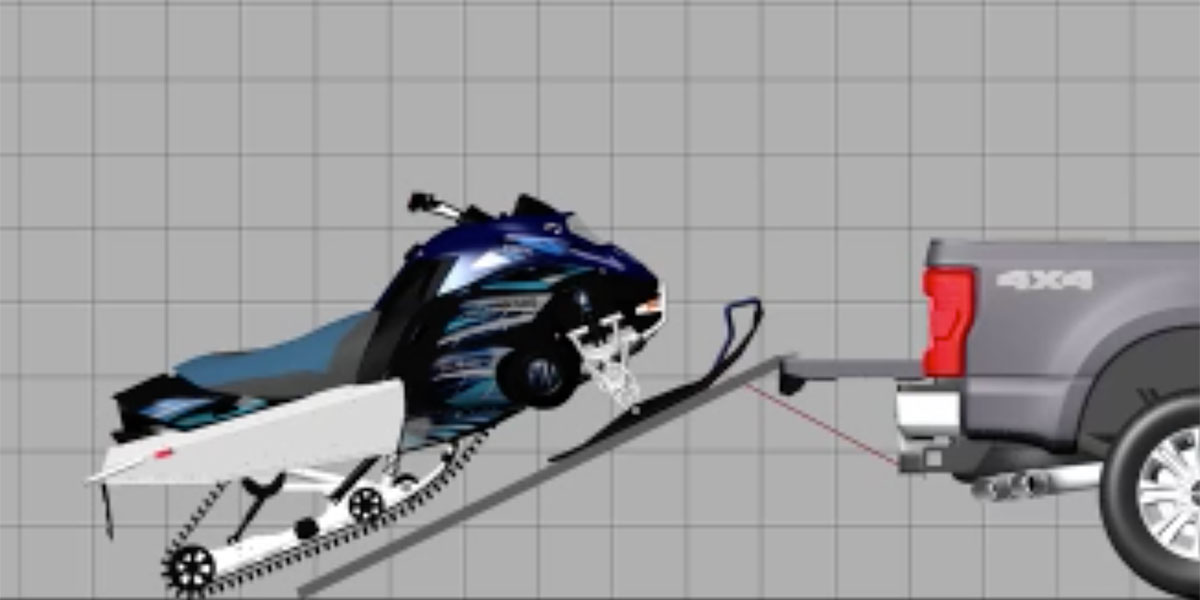
Heavy Equipment
Forklifts
Forklifts, as essential pieces of equipment in many industries, are designed with a emphasis on safety and efficiency to minimize the risk of accidents and injuries. One prevalent concern is operator crushing injuries, which can occur when a forklift tips over or collides with another object. To address this issue, manufacturers have incorporated crucial safety features such as overhead guards, seatbelts, and stability-enhancing counterweights. Additionally, the innovative third post design has been developed to further improve operator safety. This design consists of a third structural support post, usually located at the rear of the forklift, providing extra protection against lateral impacts and enhancing overall stability. By combining these safety features, the risk of operator crushing injuries can be significantly reduced.
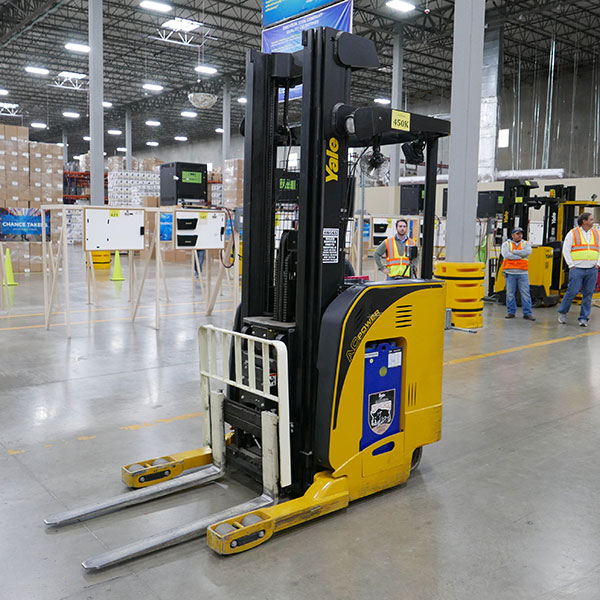
Front Loaders
Front loaders, widely used in construction, agriculture, and landscaping, are designed with functionality and safety as top priorities. Despite their robust design, one common concern is limited visibility, as the large bucket and load arms can obstruct the operator’s view, increasing the risk of accidents involving workers or equipment. To mitigate this issue, manufacturers incorporate features like strategically placed mirrors, cameras, and proximity sensors to enhance visibility, and adhere to strict design standards to ensure optimal sightlines. Additionally, front loaders are engineered with several safety features to protect operators from crushing hazards posed by load arms. These features include load-sensing hydraulic systems that prevent unintended movement of the arms, mechanical or hydraulic locking devices to secure the arms during maintenance, and reinforced cabs that provide a protective structure in case of load arm failure.
Cranes
Cranes, indispensable in construction, shipping, and heavy industries, are designed to prioritize safety while maintaining high levels of efficiency. One critical concern in crane operations is the overtipping moment, which occurs when the crane’s load exceeds its capacity, causing instability and the potential for catastrophic collapse. To address this issue, manufacturers incorporate advanced safety systems, such as load moment indicators and rated capacity limiters, which monitor the crane’s operating conditions in real-time and alert operators if the load approaches or exceeds the allowable limits. Moreover, the design of cranes is governed by rigorous engineering standards that ensure structural integrity and stability during operation. These standards take into account factors such as wind loads, dynamic forces, and material fatigue, and they mandate regular inspections and maintenance to minimize the risk of structural failure.
Falling loads pose another significant risk, which can be mitigated through the use of fail-safe load holding devices, regularly inspecting and maintaining lifting gear, and ensuring that operators adhere to proper rigging techniques.
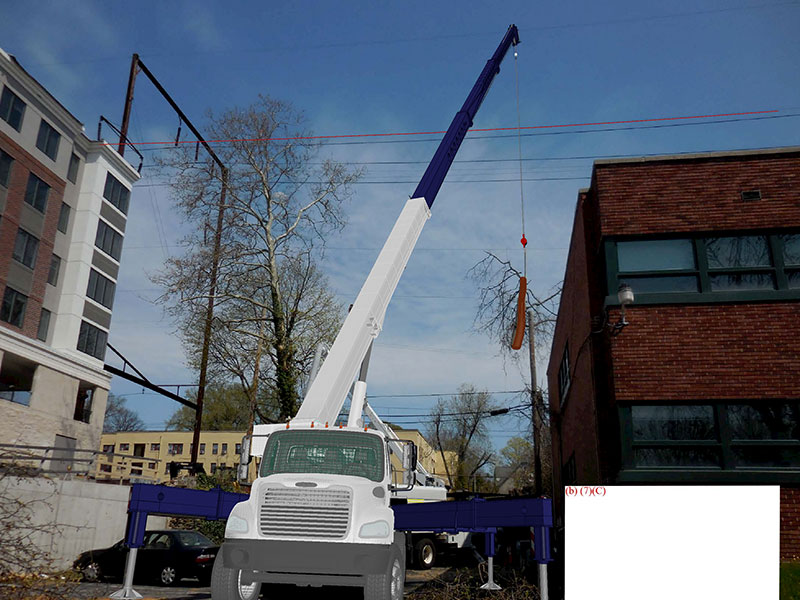
Skid Steers
A skid steer loader is a versatile piece of heavy equipment widely used in construction, agriculture, and landscaping industries due to its compact size and maneuverability. It can perform various tasks by using different attachments, such as digging, grading, lifting, loading, and snow removal.
One of the primary benefits of a skid steer loader is its versatility. However, use of the machine can lead to serious hazards, including tipping, rollovers, and crushing accidents. One of the most significant dangers associated with skid steer loaders is the potential for being crushed by the load arm.
Operators must ensure that no one is within the machine’s work area before moving it. They must also be aware of the machine’s load capacity and follow the manufacturer’s guidelines for safe operation.
Skid steer loaders are a valuable tool for many industries, but they require proper training, maintenance, and proper design precautions to prevent the associated risks.
Aerial Lift Equipment
Scissor Lifts
Scissor lifts, versatile aerial work platforms used across various industries, are designed with a strong focus on safety and operational efficiency. One primary concern in scissor lift operations is the risk of falls from height, which can result in severe injuries or fatalities. To address this issue, manufacturers equip scissor lifts with guardrails and toe boards, creating a secure perimeter around the platform. Additionally, operators are often required to wear personal fall arrest systems, such as harnesses and lanyards, as an added layer of protection. Another significant hazard is crushing from overhead structures, which can occur when the lift is raised too close to an obstacle. To mitigate this risk, scissor lifts are designed with features like height limit sensors and proximity alarms, which alert operators when the platform is nearing an obstruction. Furthermore, scissor lift designs must adhere to stringent safety standards and guidelines, ensuring that the equipment provides a stable and reliable work platform. Adequate operator training and adherence to safety protocols are essential in preventing accidents and maintaining a safe working environment with scissor lifts.
Bucket Trucks
Bucket trucks, essential aerial work platforms in industries such as utilities, telecommunications, and tree care, are engineered with a strong emphasis on safety and operational effectiveness. One primary concern in bucket truck operations is the risk of falls from height, which can lead to serious injuries or fatalities. To address this hazard, manufacturers design bucket trucks with secure, high-sided buckets and anchor points for personal fall arrest systems, such as harnesses and lanyards, ensuring operator safety at elevated heights. Operator protection from overhead crushing injuries is also of paramount importance, and bucket trucks are equipped with reinforced buckets and load-sensing hydraulic systems to minimize the risk of structural failure or overload. Additionally, to prevent tip-overs, bucket trucks are designed with boom outrigger interlocks, which ensure proper deployment of the stabilizing outriggers before the boom can be elevated. These interlocks work in conjunction with load moment indicators and other safety systems to maintain stability and prevent accidents.
Boom Lifts
Boom lifts, widely used aerial work platforms across various industries, are designed with a strong focus on safety and operational efficiency. One critical concern in boom lift operations is stored energy hazards, which can occur when potential energy is unintentionally released, causing sudden, uncontrolled movement of the boom. Another significant hazard is operator ejection from the platform during abrupt movements or impacts. Manufacturers address this issue by designing boom lifts with high-sided platforms, guardrails, and anchor points for personal fall arrest systems, such as harnesses and lanyards, providing a secure working environment for operators. Additionally, prevention of tip-overs is crucial, and boom lifts are designed with features like outriggers, automatic leveling systems, and load moment indicators to ensure stability and alert operators if the lift is nearing its capacity limits.
Machine Guarding & Industrial Accidents
Emergency Stop
Emergency stop buttons are critical safety features in machine design, intended to provide a quick and reliable means of halting the operation of a machine in the event of an emergency. They are typically prominently located and easily accessible and are designed to be easy to identify and operate under high-stress conditions. When activated, emergency stop buttons typically interrupt the flow of power to the machine, bringing it to an immediate stop. This can help prevent accidents and injuries, as well as minimize damage to the machine itself. It is crucial that emergency stop buttons be designed and implemented according to relevant safety standards and regulations, and that they be regularly tested and maintained to ensure they function properly when needed.
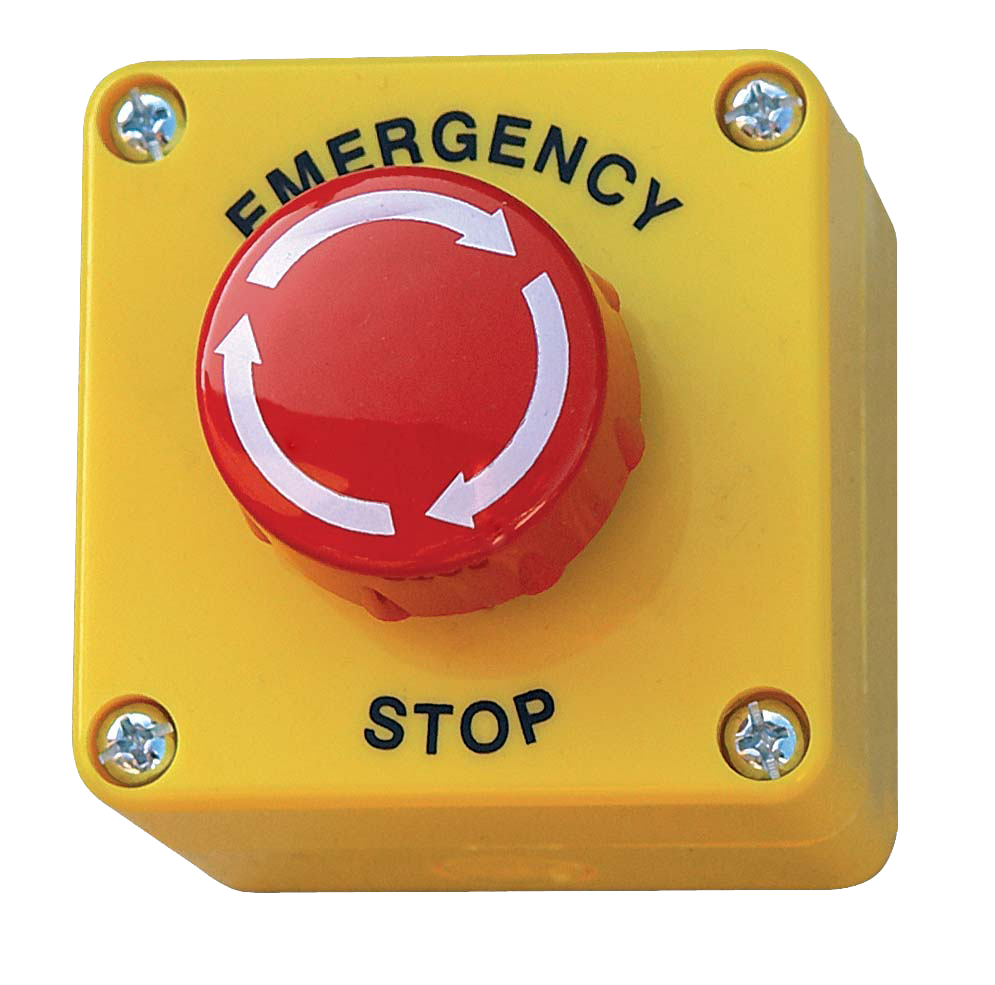
LOTO (Lockout/Tagout)
Lockout/Tagout (LOTO) is a safety procedure used in industrial settings to ensure that dangerous machines are properly shut off and not started up again until maintenance or repair work is complete. The purpose of LOTO is to prevent accidents and injuries caused by the accidental startup of machines during maintenance or repair work. Injuries are prevented by locking or tagging out the machine’s power source and disabling its energy sources, such as electrical, hydraulic, pneumatic, or mechanical energy.
The role of LOTO in machine maintenance is crucial to ensuring the safety of workers who are performing maintenance or repair work on industrial machines. When a worker performs maintenance on a machine, it is essential to ensure that the machine is in a safe condition and cannot be accidentally started up. This is where LOTO comes into play. By locking or tagging out the machine’s power source and energy sources, the machine is rendered inoperable, and maintenance workers can work safely without fear of injury from unexpected machine movement. The use of LOTO in machine maintenance is an important safety measure that should be taken seriously by all industrial employers and workers.
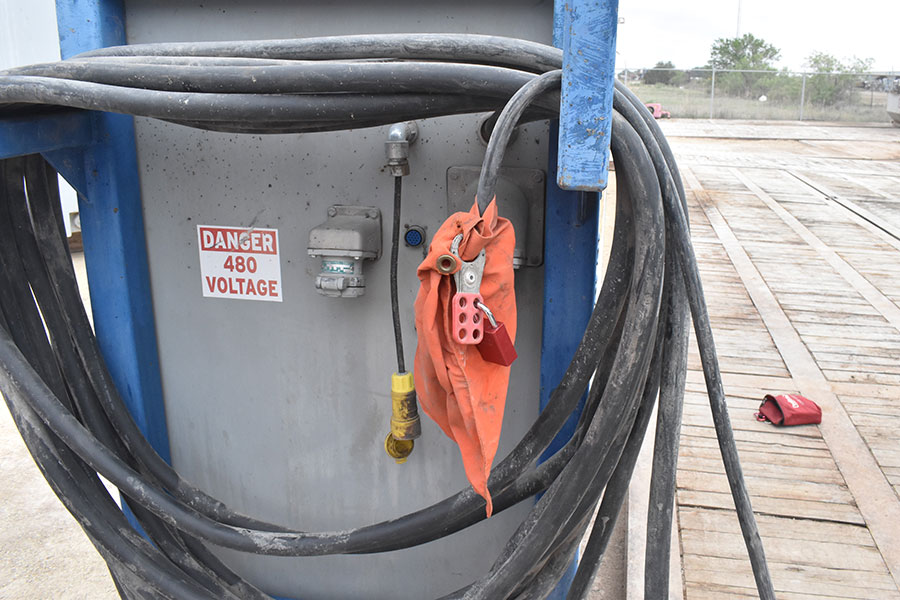